|
Industrial Electronics Design: Communication
Interface
|
Date: 25/07/2013
High performance 4–20mA current-loop transmitter for industrial electronics
By: Yuriy Kurtsevoy, Strategic Applications Engineer,
and Stuart Smith, Product Definer, Maxim Integrated
Introduction
The 4–20mA current loop has been widely used as an analog
communication interface in industrial applications. It facilitates
transmission of data from remote sensors over a twisted-pair
cable to a programmable logic controller (PLC) in a control
center. Simplicity, reliable data transfer over long distances,
good noise immunity, and low implementation cost make this
interface well suited for long-term industrial process control
and automated monitoring of remote objects.
To no one’s surprise, industry is evolving just like all
electronic applications today. It has more stringent demands,
new requirements for higher accuracy; lower power; reliable
operation over an extended -40°C to +105°C industrial temperature
range; added security and system protection; and implementation
of the digital Highway Addressable Remote Transducer (HART®)
protocol. Collectively, these requirements make the design
of today’s 4–20mA current loop quite challenging.
This article explains how to develop a 4–20mA current-loop
transmitter, analyze its performance, and select the components
that meet rigorous industrial requirements. Test data for
error analysis, overtemperature characterization data, schematics,
and analysis software are provided.
Principles of Operation and Key Design Parameters
We start by focusing on the new reference design. The block
diagram in Figure 1 shows the high-performance, low-power,
4–20mA current-loop
transmitter that reduces component count and yields the
best results for price versus performance.
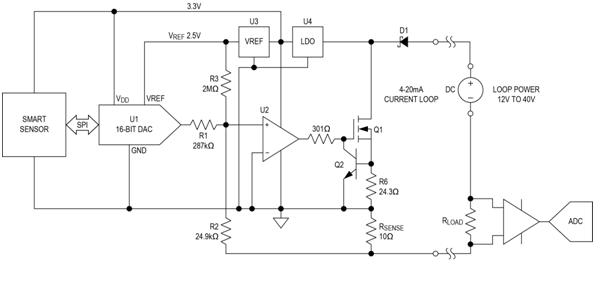
Figure 1. Reference design for a 4–20mA loop-powered
transmitter features the MAX5216 16-bit DAC (U1), the MAX9620
op amp (U2), the MAX6133 voltage reference (U3), and the
MAX15007 LDO (U4).
This reference design uses low-power, high-performance components
that provide less than the 0.01% at 25°C and less than 0.05%
over the temperature range for industry’s most demanding
4–20mA current loop. The design features a low-power 16-bit
DAC (U1), a zero-drift rail-to-rail input/output (RRIO),
high-precision op amp (U2), a voltage reference (U3), and
a 40V low-quiescent-current LDO (U4).
The U3 voltage reference provides low noise, low temperature
drift of 5ppm/°C (max) and a precise 2.500V for U1. The
smart sensor microcontroller commands U1 through a 3-wire
SPI bus. The U1 output is divided and converted to the loop
current by the Q1 power MOSFET, 10 ohms(±0.1%) sense resistor
(RSENSE), and U2. The U1, U2, and U3 devices are powered
by U4, which is powered directly from the loop. There is
a current-limiting circuit made with Q2, a BJT transistor,
and sense resistor (R6). This circuitry limits the loop
current to approximately 30mA, which prevents runaway conditions
and any damage to an ADC on the PLC side. The Schottky diode
(D1) protects a transmitter from reverse current flow.
Observations About Design Performance
The reference design operates at low power. The maximum
current consumption of the selected components is less than
200µA at +25°C and less than 300µA over the -40°C to +105°C
temperature range. The U2 op amp has a 25µV (max) zero-drift
input offset voltage over time and temperature, so it is
ideal for the accuracy and stability requirements of the
application. The 10 ohms current-sense resistor allows operation
with a low loop-supply voltage; its smaller resistance dissipates
less power and allows use of a smaller package, which further
shrinks this transmitter. For example, if only a 10 ohms
RSENSE and 10 ohms load are present, then the maximum voltage
drop on them at 30mA is 600mV. The U4 LDO requires only
4V for proper operation with a 3.3V output, and the total
minimum loop supply can be as low as 5V. However, if the
PLC load is 250 ohms, then the minimum loop supply must
be 4V + 30mA × (10 + 250)ohms = 11.8V.
Note that to determine a more accurate estimation of the
minimum loop supply voltage, the loop cable resistance must
also be considered.
During testing the output exhibited some noise at 10O. Increasing
the value of the RSENSE resistor will increase power dissipation
and a minimum loop supply voltage, but it will also reduce
noise on the loop. This is a trade-off that the user can
control.
The U2 op amp tracks the voltage drop across R2 and RSENSE,
and maintains 0V at both of its input nodes. The following
equations are used for this circuitry:
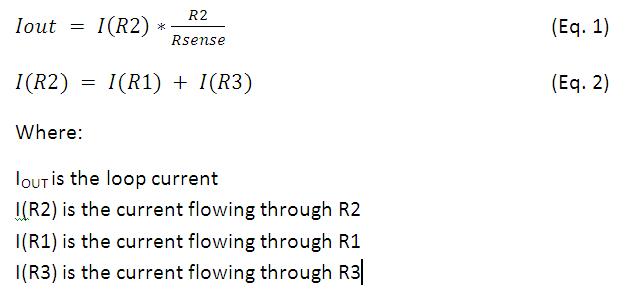
In Equation 2 we assume that the input current to IN+ and
IN- of U2 is 0. Following Equations 1 and 2, the initial
loop current of 4mA is set by the I(R3) current while I(R1)
is 0. Therefore:
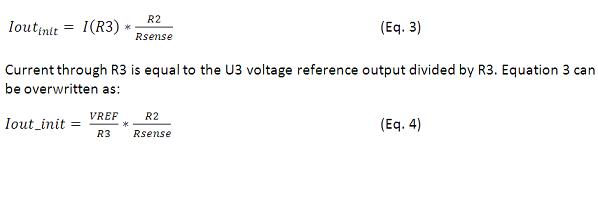
According to the Namur NE43 recommendations for failure
information transmitted over a 4–20mA current loop, the
signal range for measurement information is from 3.8mA to
20.5mA, allowing for a small amount of linear overrange
process readings. In some cases when additional failure
conditions are defined, an even larger dynamic range is
required for the loop current, for example, from 3.2mA to
24mA. Thus, selecting R2 = 24.9k, IOUT_INIT = 3.2mA, and
solving Equation 4 for R3 yields:

A 1.945 M Ohms resistor is costly and, perhaps more important,
not well suited either for automated production or for easy
field calibration. Therefore, it is preferable to use a
regular 1% tolerance resistor and regain accuracy by calibrating
out the 4mA offset current and the 20mA full-scale current
with the U1 DAC. In this case, some digital codes are needed
for calibration to ensure the required accuracy. Thus, I(R1)
= VDAC/R1, where VDAC is the U1 DAC output voltage. This
can be rewritten as:
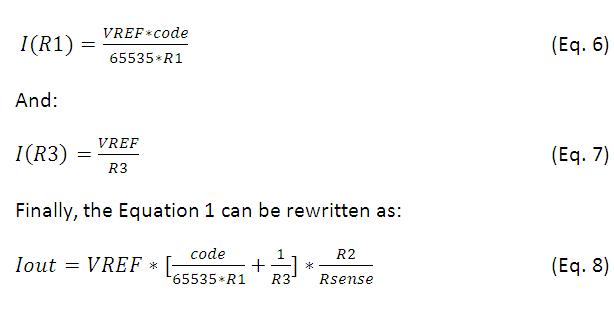
Error Analysis and Performance Optimization
Transmitter Error at +25°C
Table 1 presents the error analysis of the passive components
and VREF in the 4–20mA current-loop transmitter at +25°C.
Data are based on Equation 8.This table is available for
download and the designer is encouraged to use the What-If
Analysis/Goal Seek… feature from the Data tab to find the
appropriate codes for 4mA, 20mA, and 24mA IOUT.
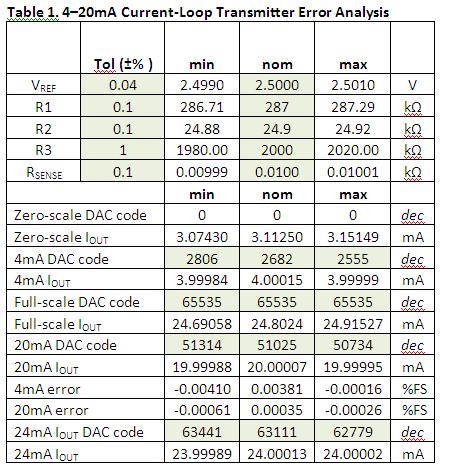
Thus, having the standard 1% tolerance 2M ohms R3 resistor
and setting the U1 DAC to 2682 decimal code, the initial
loop current of 4.00015mA is maintained. Note that the total
calculated error is much less than the tolerance of the
individual components because their errors are calibrated
out by the high-resolution U1 DAC.
The effective number of bits (ENOB) of a 4–20mA current-loop
transmitter can be calculated as:

Based on the data from Table 1, the ENOB is equal to 15.56
bits. So, dropping less than 0.5 bit of the total resolution
allows the calibration process to be automated and lowers
the number of expensive precision components.
The selected resistors in Table 1 cover the current loop’s
dynamic range from 3.2mA up to 24.6mA. Different combinations
of R1, R2, R3, and RSENSE can shrink the dynamic range.
Close attention should be paid to the temperature coefficients
(TC) for each resistor.
Transmitter Error Overtemperature Analysis
The overtemperature error analysis of the passive components
and VREF is shown in Table 2.
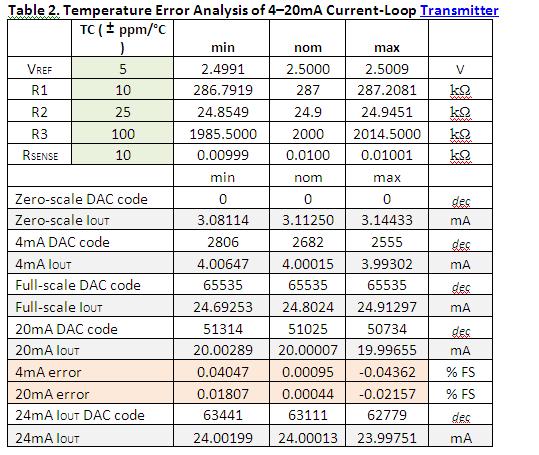
The following formulas are used to calculate the minimum
and maximum resistance drift:
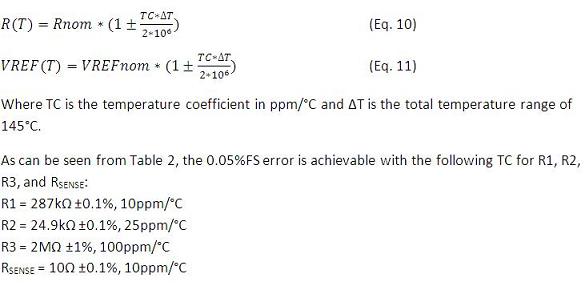
Note that total error is the square root of the sum of the
squares of each source of error: component’s tolerance,
component’s tempco, measurements, etc.
If a smart sensor consumes more than 3.4mA, it cannot be
used as part of a loop-powered 2-wire transmitter. This
happens, for example, when a microcontroller or ADC consumes
more than 3mA or when a sensing element requires a higher
supply current to increase its dynamic range and/or resolution.
In such cases, the extra current has to flow through an
additional third wire. This configuration, called a 3-wire
transmitter, can be modified as shown in Figure 2. This
design makes it universal as a 2- or 3-wired smart sensor
transmitter.
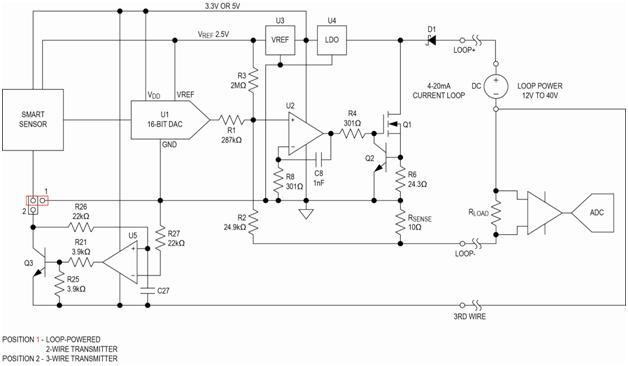
Figure 2. Block diagram for a universal 2- or 3-wire
smart sensor transmitter.
The U5 op amp and Q3 buffer in Figure 2 are sensing the
virtual ground, continuously maintaining the common point
for the smart sensor and keeping it at the constant voltage
of the U4 output. The U5 op amp must be capable of accepting
a maximum supply voltage of 12V with a PLC RLOAD/sense resistor
value up to 250 ohms. The C8 and R8 negative feedback network
stabilizes the loop current and assures stability for all
normally expected loading conditions.
Selecting the Power Transistor and Protection Components
There are no special requirements for the Q1 power transistor.
It could be either a MOSFET or bipolar power transistor
which satisfies maximum safe, operating area criteria. For
example, if the loop power supply is 36V and the highest
limiting current is 35mA, then the maximum dissipation requirement
is 1.26W. Close attention should be paid to proper layout,
traces width, and the heatsink capabilities of the PCB.
The Schottky diode (D1) (see Figure 1) is a safety device
to prevent any damage to the transmitter from reverse current
flow. In addition, a transient voltage suppressor (D2, not
shown in block diagram) can be added between the LOOP+ and
LOOP- inputs to protect from overvoltage surge conditions.
The requirements for D1 and D2 depend on the safety standards
of the application.
Testing the Design
A 4–20mA loop-powered transmitter evaluation (EV) kit, the
MAX5216LPT, was built and characterized with a 1000ft 22-gauge
shielded communication cable and load resistor of 249O ±0.1%.
The loop current was measured with an Agilent® HP3458A DVM
as the voltage drop across that load resistor. The characterization
data from the MAX5216 DAC are presented in Figures 3 to
8.
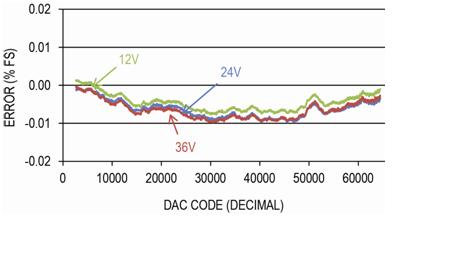
Figure 3. Transmitter error at 25°C. Data for MAX5216
DAC.

Figure 4. Transmitter error change vs. temperature
with a 12V loop supply.
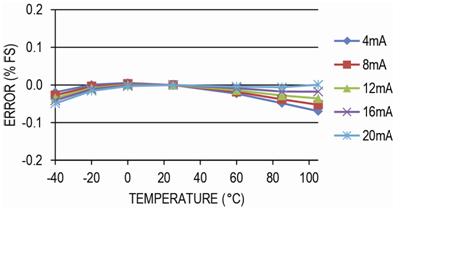
Figure 5. Transmitter error change vs. temperature
with a 24V loop supply.
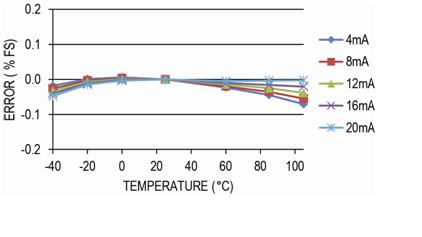
Figure 6. Transmitter error change vs. temperature
with a 36V loop supply.
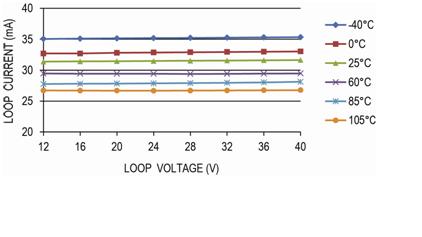
Figure 7. Current limit vs. loop voltage with a 24.3O
sense resistor.
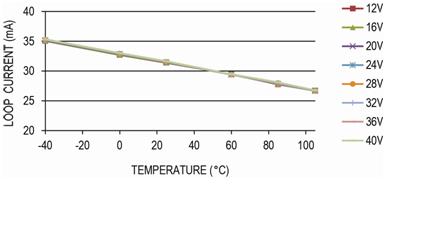
Figure 8. Current limit vs. temperature with a 24.3O
sense resistor.
This transmitter reference design also supports the HART®
protocol. It allows simple connection with a HART modem
such as the DS8500 (see Figure 11). Figures 9 and 10 show
HART signals over a 1000ft 4–20mA current loop with a 249
ohms load resistor.
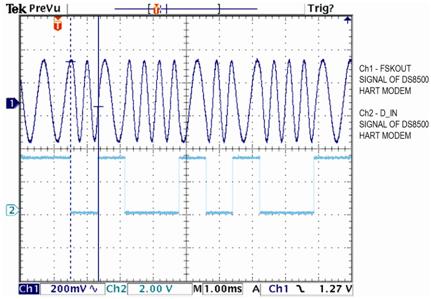
Figure 9. HART communication over 4–20mA current
loop.
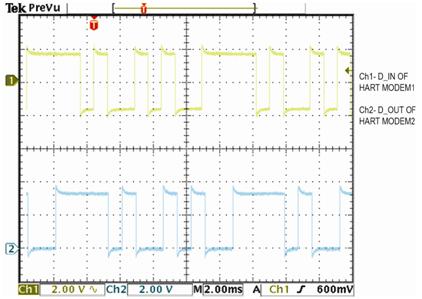
Figure 10. HART communication between two modems.
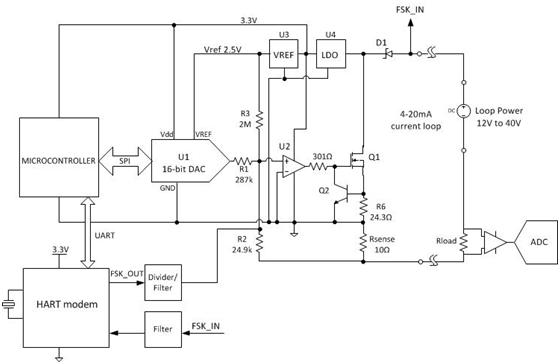
Figure 11. Block diagram with HART modem
Agilent is a registered trademark and registered service
mark of Agilent Technologies, Inc.
HART is a registered trademark of the HART Communication
Foundation.
About the Authors
Yuriy Kurtsevoy is a senior strategic applications engineer
with the Industrial Measurement BU in the Industrial and
Medical Solution Group at Maxim Integrated. He joined Maxim
in 2011. He holds an MS in honors electrical engineering
from the East-Ukrainian National University, Luhansk, Ukraine.
Stuart Smith joined Maxim Integrated in 2011 as a Product
Definer. He has worked for over 30 years as an analog and
mixed-signal IC design engineer and has received eight patents
during that time. Mr. Smith has a BSC EE from Abertay University
and is a Chartered Engineer.
|
|
|
|